It is fascinating how some concepts from sports or the military can be applied to business to achieve higher results with less effort. Among these is an idea I came across years ago when I was first learning Brazilian Jiu-Jitsu.
If you are not familiar with Brazilian Jiu-Jitsu, it is grappling heavy and typically involves a strategy of getting close to an opponent to avoid their strikes and then taking them down to the ground and controlling them using a variety of submission techniques. An experienced Jiu-Jitsu instructor was once talking about becoming skilled at these techniques, and he said, “Stop trying to hurry up when you are doing your practice. Remember: slow is smooth, and smooth is fast.”
“How can slow and smooth be fast? That doesn’t seem to make sense,” I asked, confused.
“When you start out, you will want to try very hard, and this will make your muscles tense from resistance, so you will exhaust quickly,” he said. “Later, when you learn to relax and flow with the movement it will naturally be much faster, but only as fast as it needs to be. Timing and not wasting energy are more important than speed.”
Turns out this saying was adopted from some Navy Seals who were training at the same gym, it being a commonly used term among Seal teams. The fundamentals of this philosophy are also applicable to many of the processes involved in screen printing and apparel decorating in general. There are several ways to think about it, but some of the most relevant pertain to waste and energy conservation. To focus on improving those areas and making them smoother, i.e., reduce resistance or friction, we first deconstruct them and then look at the parts that contribute to the process as a whole. That done, we can reassemble them to achieve better flow and higher productivity.
Less Motion, Greater Efficiency
A basic principle of efficiency is addressing the micro first and then reflecting back on how this affects the overall, larger process. To start out then, what do we mean by waste when it comes to screen printing? That by itself can be a bit of a pandora’s box, because there are lots and lots of potential areas that either produce or contribute to waste in printing. It is therefore useful to categorize them first into process waste, and component or product waste.
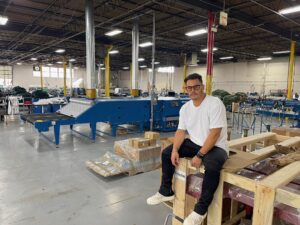
Rich Santo of Chicago’s Culture Studio, where doing things right comes first, efficiency second and speed comes as a natural consequence. Photo by Thomas Trimingham
Process waste can include things related to tasks, movements, staging steps and transporting or adjusting processes. If there are excess steps being done to prepare screens, fold and stack shirts, load ink into the screens or even just load each shirt onto a pallet, these all represent waste that can be reduced. Bear in mind that getting rid of the unneeded is often more effective than adding something extra. In some cases, a process can be automated or even eliminated entirely depending on whatever technology you may have in hand.
To pick a specific example, has your shop ever tried to figure out the most efficient way of loading garments to be printed? Most shop owners and operators would say they know what the best process is already. The interesting thing, though, is how much a simple thing like loading shirts can vary from one operator to another. Some printers like the garments to be stacked with the side to be printed facing down. Others prefer them facing up. Still others prefer to have their shirts off to the right or directly behind them.
The point here isn’t to say which group is right, but to look at the results they achieve. If, for example, you measured the method that is consistently less tiring to the loader and has the least tendency to distort the garments being decorated, you will probably have a winner. The technique that ends up being your own “best practice” will also probably require the least steps and the least twisting of the torso or bending at the waist. When you’re decorating hundreds of shirts even these kinds of little extra wasted motions add up.
On a side note: one of the fastest, most efficient T-shirt loaders I have ever seen employed an “under the armpit” style. The garments were stacked behind her on a cart equipped with a foot pedal that would raise the cart incrementally as the shirt stack was reduced. The operator would load by reaching across her body with her left hand and then stretch her right arm out to grab the other seam without turning around. The top garment would then be popped open in one smooth movement over the pallet and gently pulled back at the shoulders and smoothed as needed. She told me the right amount of tack on the pallet was key to doing this well. It was fast, but not rushed, with zero wasted motion or extra steps needed.
Getting Your Ink Right
Another area where manual screen printers, in particular, can improve their processes is in the area of ink. The ink that comes from most suppliers tends to be too thick out of the bucket. This is especially true of white and light-colored inks in which the pigments are heavier. Experimenting with an ink additive when working with your most commonly printed inks can make an enormous difference, especially if you have to consistently do two passes with the squeegee to get the screen to clear out. The best viscosity of ink should clear out of the screen in a single print, unless you are printing with a heavy solid or high opacity.
Another way to ease the arms and wrists of a manual printer is to add some extra EOM (or “emulsion over mesh,” which stands for the thickness of the screen stencil) to your manual screens. Adding just a little extra thickness by doing another coat on an already dried screen, for instance, can often allow you to be able to cover in one print instead of having to print, and then print again. The key is to test to get just the right amount. Not too thick! Experimenting with these kinds of efficiencies in screen making will pay off in saved time and energy.
Again, the goal in addressing process steps is to become more fluid and less wasteful, not just drive yourself and everyone around you crazy criticizing every extra step or movement. If you find something or see something that works better, makes less mistakes and uses less energy, have everyone try it out and see how things go. Leaving everyone to do things their own way may create less waves, but it won’t allow people to learn better habits and improve. There is always a way to encourage improvements using a positive mentality.
Wasted Products and Components
There are a number of ways of producing less waste in screen printing, like using a little more emulsion and a little less tape to seal screens, or optimizing your dip tank or reclaiming process to recirculate chemicals and water as much as possible.
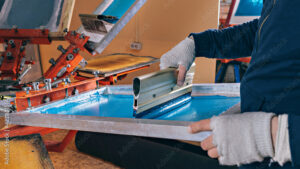
Manual screen printing, in particular, can be hard on the body. Rationalizing your process is therefore good for operators as well as profitability. Photo by photo_gonzo- stock.adobe.com
The results of these refinements can be significant and are certainly worth doing. That said, the most expensive source of product or component waste is misprinted garments. The reason this is the top problem is the fact it is magnified every time you have to re-print something, which in turn requires drawing profits from all your other orders as compensation.
During a recent visit to the rapidly expanding Culture Studio shop in Chicago, Illinois, this idea came up in a discussion with owner Rich Santo. “When we first started out, it was always push, push, push and rushing around,” Rich said. “We had some of our fastest printers going like crazy, but they would also make more mistakes. Now we focus on doing things right, getting a good flow from one step to another, and we have multiple quality control checks on every order. This has made a huge difference.”
According to Rich, “If you push your printer’s too hard about speed, even if they are successful at going fast they will burnout quick. It’s not the best strategy for long term employees.”
As evidence of this approach, whenever we passed an employee hard at work a during a walkthrough that same day there were lots of smiles and waves. There was also a wealth of signage in all areas of the screen prep and production process focusing on efficiency and productivity, not to mention plenty of equipment upgrades.
When I asked how Culture Studio has managed to address its rapid growth so effectively, Rich pointed to the many computer screens that were in evidence. “We heavily invested in our own custom order-tracking software system, so we know where every order is across both locations and the stage it’s in,” he said. The result is a process that emphasizes precision, accuracy and measurement over speed. And though they certainly had speed as well, no one seemed to be stressed about it.
Excellence Through Repetition
A critical step that works in martial arts—and business, as well—is taking the constituent parts making up a process, like shirt loading, and then breaking them down into a series of intentional moves based on what you find are your own best practices and then learning them through repetition. Most screen printers won’t
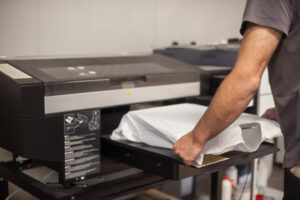
Even a procedure as seemingly straightforward as loading blank T-shirts can be improved through a combination of study and practice. Photo by guruxOx – stock.adobe.com
have a problem finding a variety of repetitive ways of loading shirts. The key to making improvements is to take the best versions of these different processes and practice them to achieve a method with the smoothest flow. Ask yourself, “Where do I feel resistance? Where could things be done more easily, flowing from one part to another?”
Using this as a guide can not only greatly improve the process itself, but make a huge difference in terms of wear and tear on operators. Pay close attention to what you are doing over the course of your next production run. After 100 shirts, stop and see if you are feeling tight in places or tired overall. This can be a clue as to how to adjust your position or the environment to get whatever friction points may exist out of the way.
A good way to think about training repetition is to visualize each repetition as a step up a ladder toward your goal. As with martial arts, if you try to rush your way through these repetitions, especially in the beginning, you will invariably end up taking steps back down as well. The reason for this is you won’t be learning to do things with a natural smoothness. This in turn will result in your final processes not being as effortless.
To really get a process down, even something as seemingly simple as loading, stacking or folding shirts, can take a while to master at a slower, careful pace. When you feel like it comes naturally without a lot of concentration, you can start to add in a little more speed. The weird thing with learning techniques this way is that often you will achieve very high speeds in the end without pushing things at all, simply because the job is now so much easier.
Reassembling Your Processes
The real power of this approach becomes evident when you put together multiple processes after evaluating and then mastering the best practices for each of them individually. If you have seen a person who has mastered the art of loading and printing manually and then watched a beginner, the difference can be shocking: not only in terms of speed, but in the way the newbie will often finish the order exhausted and with everything around them covered in ink. This is where a good screen-printing trainer would say, “It’s okay, slow it way down and try to smooth out your movements. Watch where you can make each step easier and then get into a rhythm before you try to go faster.” The speed will come as a result of becoming more proficient as the body figures out what to do, not before just by pushing it.
Less waste will come as a natural occurrence of smoother processes in many of screen printing’s other steps as well. Take for example, cleaning out screens after a long print run. This task may not be as glamorous as printing, but doing it thoroughly and efficiently is critical. Something as simple as defining a series of best practices for this necessary task will directly affect the rest of the steps after, it not only for an entire day but the week. If you own or run production at a larger shop, consider the impact a well-trained cleanup crew could have on every station. When someone feels comfortable with the process and can flow through it, not only will there be far less mess, but the results will be big timer saver for everyone involved.
Thomas Trimingham has been helping screen printers for more than 25 years as an industry consultant, artist and high-end separator, and author of over 180 articles. If you have feedback or wish to comment on this article you can reach Thomas at: [email protected].