Over the past decade, there has been an increasing trend of decorating companies launching their own lines of apparel. Along with this movement comes the need for providing customized neck labels to both personalize a company’s brand and deliver an upscale look. To meet these demands, neck label tagging decorators now have many options at their disposal from which to choose the best method for this process.
Unbeknownst to them, a lot of shops already have the ability to sew-in neck labels. However, the process is expensive and labor intensive, due in part to the fact sewn-in labels must be ordered in advance and purchased from an outside vendor. Many shops also lack the equipment and skills to install them. Granted, garments with tearaway labels can be purchased and then sent to an outside source to sew-in new labels as well. However, this slows delivery times and adds costs to the bottom line.
Having been involved with the sewn-in method during my time working at National Mills, I can attest to the fact that managing neck-label inventory can also be complicated when you have thousands of individual garment labels to keep track of. Big brands use neck labels to account for how many garments a contractor is manufacturing for them. This in turn puts pressure on decorators to account for these labels. Luckily with today’s technology, there are several options other than sewn-in, including direct screen-print, heat transfer and pad printing.
Screen Printing
Direct screen-printed neck labels can be printed on a manual textile press or an automatic press for larger-quantity orders. When using a manual press, a sleeve board or koozie platen works well for this application. However, tackling larger runs using a manual press can be time consuming and labor intensive.
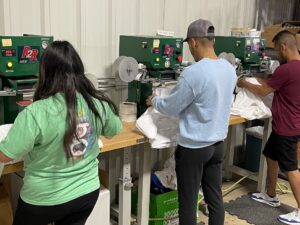
HIX R2R label presses provide efficiency for shops that take on larger orders. Photo courtesy of Geneologie LLC.
An option for decorators facing this situation is purchasing a small-format automatic tag printer designed specifically for printing neck labels. These machines are similar to a standard automatic screen press and take up a much smaller footprint, making them the perfect solution for screen-printers who already understand the fundamentals of screen-making.
For those interested in this approach, Wally Klejka of T&J Printing Supply, based in Huntley, Illinois, recommends the M&R Copper Head Pro Mini tag printing press: a piece of equipment his company not only distributes but provides service and training for to ensure customers understand how best to load, print and unload garments for maximum label-printing output. According to Klejka, one of the features he really likes with this machine is the fact it’s all electric—no compressed air needed. It can also produce up to 2,160 pieces an hour!
Again, neck labels can also be screen-printed on a standard automatic press; although the process is much slower since the garment needs to be turned inside out and printed on the inside neck area and then dried in a textile dryer. That said, to avoid having to turn the garment inside out—and thereby speed things up—Action Engineering offers the option of a shirt platen expressly designed for printing neck labels on an automatic press by allowing operators to load the garments in such a way that the neck area is folded back for printing.
According to Action Engineering’s Erik Naftal, the company’s “label pallet,” as it’s called, has been a game changer for screen printers not yet ready to go with a dedicated tag printer by reducing the amount of handling needed. “The label pallet was designed as a double three-way pallet that allows two garments to be loaded for neck label printing…the pallet can (also) be rotated 180 degrees to use the three cutaway positions on the pallet designed to print pockets and koozies,” Naftal says.
Heat-Transfer Labelling
As for screen printers, they have the option of printing their own neck label transfers by ganging the artwork on a screen, screen printing a full sheet of plastisol transfer labels, and then cutting the transfers apart and applying them to the garment with a small-format heat press. Pre-printed, direct-to-film (DTF) transfer labels are another option for those using this approach. Note: a hat heat-transfer press can also often be used for applying neck labels. Most heat-press manufacturers offer small-format heat presses as well, presses specifically designed for applying neck labels, patches and other small heat-transfer graphics.
Another option is a roll-to-roll heat press that uses heat-transfer labels created on a continuous web screen print line purchased by the roll, typically in rolls of 500. The machine applies each transfer under high pressure in three seconds or less after which it advances to the next transfer. There are safety features built into the machine to keep the operator’s hands away from the heat platen during pressing.
John Wacob of Geneologie LLC is a big fan of the roll-to-roll label operation. “We run three HIX roll-to-roll neck label heat-transfer machines, and we can output 1,200 garments per hour. I was drawn to this process, because I like the crisp clean look a heat-transfer label offers.”
Pad Printing Garment Lables
Pad Printing was originally developed for printing on objects like pens, golf balls and other small plastic items. The pad printing process employs a metal plate etched with the graphic to be printed and a doctor blade that floods ink across the etched plate filling the image area with pigment. Next, a rubber pad compresses onto the plate picking up the inked image, which is then stamped directly to the neck area of the garment.
The ink used for the pad printing process was not originally made for printing on textiles, but it works well on small image areas. Always consult with the manufacture on ink recommendations for this application to ensure washability. For pad printing labels on dark garments, the ink color used is typically gray as opposed to white for best results.
Whether you invest in sewing equipment and provide sewn-in neck labels, purchase a small-format automatic press, offer pad printing or use heat transfers, now is the time to research and ramp up private label tagging and get on board with this increasingly popular trend in apparel decoration.
James Ortolani has 40 years of experience in the decorated apparel industry, specializing in hands-on, direct screen printing and heat-transfer production. For more information or to comment on this article, email James at [email protected].