Starting anything new can be overwhelming. We are all bound to make mistakes. So, sit down and take three deep breaths. Feeling better? Good. To save you some time, I want to share five common mistakes many embroiderers make when starting their embroidery journey. These mistakes have happened to most embroiderers at one time or another, but avoiding them is essential to starting off on the right foot.
1) Not Knowing Your Fabric Limitations
As an embroiderer, it is crucial to know the limitations of your fabric and the best way to embroider it. First, the thinner and stretchier your fabric, the fewer stitches and less dense your design should be. Otherwise, if the design is too heavy (dense) for the fabric you are embroidering, you may get puckering. If, on the other hand, the fabric you are working with is heavier or thicker, your design can be denser. These kinds of heavier fabrics need stabilizers for the hooping and embroidery process only.
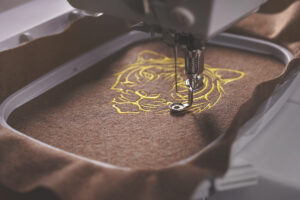
Different fabrics need different needle types and backing. Photo by R_boe – stock.adobe.com
Another critical point is ensuring you have the correct backing. There are a range of different kinds of backing you can use depending on the fabric you’re working on. Cut-away backing is typically used for stretchy knits and light woven fabrics. Tear-away backing is best for heavier woven fabrics, such as twill, denim and canvas. Heat-away backing is another alternative to traditional backing for lace, organza and sheer fabric, being a type of backing that can be quickly and easily removed using a household iron or similar heat source. Lastly, specialty backings, such as washaway backing, can be used for projects involving applique or freestanding lace.
2) Not Checking Your Tension Settings
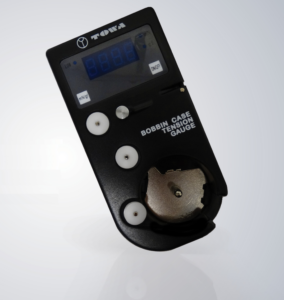
Tools like this Towa tension gauge can help avoid top-stitch looping and thread breaks. Photo courtesy of Madeira USA
Poorly set thread tensions can result in unsightly bobbin thread showing up on top of the embroidery, top-stitch looping and thread breaks. Top thread tension settings vary by thread type. Fabric type and the idiosyncrasies of the machine (or machines) you may be running should be taken into account as well. The best practice is to run tension test designs with the different thread types you use to determine where your particular machine’s optimal tensions fall. Adjusting the bobbin tension before setting your top thread tensions is essential. The reason for this is because a multi-needle commercial machine has a single bobbin and bobbin case that works with each needle.
Also be sure and check the tension on your bobbin thread each time you replace your bobbin. Bobbin case tensions should fall between 25 grams-force/inch, or gf, and 35 gf. When doing so it’s a good idea to use a Towa-brand digital bobbin tension gauge in order to get accurate readings for both top and bottom thread tensions.
3) Not Changing Your Embroidery Needles for Different Projects
Did you know that eight hours of running time is the optimal lifespan of an embroidery needle? Worn needles can result in thread breaks, skipped stitches and shredded threads. The look of your embroidery can be instantly improved by replacing worn needles with fresh ones. Also, it’s vital to remember that needle sizes and point types must be considered for each thread and project. Ballpoint needles are designed for use with stretchy knit fabrics like T-shirts, performancewear, polos and light wovens. Sharp points are best for tightly woven garments that are heavy and dense, such as twill, denim, ball caps, backpacks, leather and vinyl. It is also important to note that the thicker your thread is, the bigger the needle you will need in order to accommodate the thickness of the thread through the eye of the needle as well as to open an appropriate-sized penetration hole in the fabric.
4) Not Being Careful with Embroidery Design Placement
Proper design placement will come with practice. In the meantime, it is important to measure your garments and mark with a fabric pencil where the design will look best.
A great way to accurately measure design placement is by aligning your design with the help of a guide, like the All-In-1 Hooper available through my company, Madeira USA, a valuable piece of equipment that makes fast and accurate work of proper placement on garments of all sizes. For embroiderers who mainly do shirts, in particular, the guide is a great tool to have. Holding off on splurging for a substantial piece of hooping equipment? Never fear. There are placement charts you can find online a well.
5) Not Prioritizing Machine Maintenance
In order for your embroidery machine to run seamlessly (no pun intended), you must maintain it daily. Here are my suggestions:
- Keep your workstations tidy and clean; this will reduce the chance of things like oil spills and prevent the buildup of excess lint or any soiling that may occur
- Lubrication is a MUST to prevent parts from wearing down too quickly; I recommend referring to your machine manual recommendations; Hook Wash (a mineral based lubricant/solvent mixture also available from Madeira USA) can help with quick and easy cleaning and surface lubrication
- Regularly clean your rotary hook area using compressed air
- Remove the needle plate and clean often; compressed air and a round brush can help with this job
- Check the thread path regularly to ensure there is no lint buildup or burrs on the needle
- Clean your metal bobbin case and clean underneath the metal tension flap.
And that’s it! Well, not exactly. There’s plenty more to know and take care of when it comes to quality machine embroidery. Nonetheless, ensuring you’re not making these five common mistakes is a great way to build a solid foundation upon which to begin your embroidery journey.
This article has been adapted from an educational blog piece originally created by Abby Gordon, digital marketing coordinator for the thread and machine embroidery supply company Madeira USA. For more great articles by Madeira, go to madeirausa.com/blog/education. To check out Madeira’s complete line of threads, bobbins, backings and commercial machine embroidery accessories, including the All-In-1 Hooper and Towa gauge mentioned as a part of this story, go to madeirausa.com.