Every custom decorator has been there—you open the heat press and discover a press mark, discoloration or even a ruined garment. This can be especially frustrating when working with today’s performance wear and premium synthetic fabrics, which are popular for their lightweight feel and modern appeal but are also more sensitive to heat. Whether it’s a high-end performance fabric turning yellow or a scorch box on a premium tee, these mishaps can feel like setbacks.
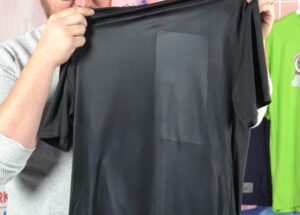
Though it can be a problem when working with performance apparel, with the right techniques and tech, scorching can be eliminated, even on tricky fabrics. Photo courtesy of STAHLS’ Transfer Express
But don’t worry—scorching doesn’t have to be the end of the story. Heat printing is one of the most versatile and efficient decoration methods around, offering quick turnaround times, customization and the ability to decorate nearly any fabric or design location, including those other methods decorators struggle with as well. With the right knowledge and techniques, you can prevent heat-related damage and keep your garments (and reputation) intact.
This guide will break down why scorching happens and provide practical tips to help you achieve flawless, scorch-free heat printing every time.
How Heat Press Scorching Happens When Heat Press Decorating
To address the issue, we first need to understand what scorching is. Simply put, scorching occurs when garments—especially those made with synthetic or plastic fibers, like polyester—are exposed to excessive heat or pressure during the heat-printing process. The result can range from a visible press box or shiny fabric to discoloration or even a burnt garment.
At its core, scorching happens because the fibers in the fabric begin to melt or degrade under high heat. The reaction can differ depending on the garment material, making it essential to recognize how different fabrics respond to higher temperatures. Whether it’s polyester, nylon or the newest trending synthetic material, knowing how to prevent scorching allows businesses to protect their bottom line while minimizing waste.
For decorators, scorching isn’t just an annoyance, it can directly affect profits. Sending out garments with press boxes, burns or discoloration can lead to dissatisfied customers, tarnished trust and even lost business.
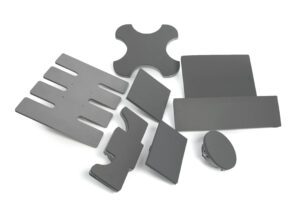
Smaller platens can be useful for isolating print areas, thereby reducing the risk of scorching the surrounding fabric. Photo courtesy of STAHLS’ Hotronix
Yet, the solution isn’t as simple as just lowering the temperature. Heat transfers require precise settings—time, temperature and pressure—to adhere properly and ensure longevity through wash and wear. Lowering the heat too much risks producing garments that appear fine initially but crack, fade or peel after repeated use, damaging your reputation as a reliable decorator.
Maintaining quality and customer satisfaction requires balancing these factors while taking steps to prevent scorching before it happens.
In addition, preventing scorching is not just about preserving the quality of individual garments, it also plays a role in reducing waste and promoting sustainability in the heat-printing industry. In a world and in an industry that have become increasingly aware of the environmental impact of fast fashion, every wasted garment contributes to the growing problem of textile waste in landfills.
By mastering techniques to avoid scorching, apparel-decorating businesses can minimize the number of misprinted or damaged items, extending the life of the apparel and reducing the need for replacements. This approach in turn aligns perfectly with broader efforts to create a more sustainable future, where quality and care go hand in hand with environmental responsibility.
Best Practices for Preventing Scorching When Decorating with Heat Transfers
Preventing scorching starts with understanding your materials and the decoration method you’re using. Certain fabrics, like polyester and tri-blends, are more prone to scorching due to the nature of the synthetic fibers they employ. Dark-colored polyester, in particular, tends to show visible press marks. When working with these materials, consider whether the decoration method requires high heat and, if so, adjust your approach accordingly.
Choosing low-temperature transfers, such as direct-to-film (DTF) or heat-transfer vinyl that applies below 300°F, can significantly reduce the risk of scorching. These transfers are ideal for heat-sensitive fabrics like performance wear, as they allow you to maintain quality without compromising the garment’s integrity.
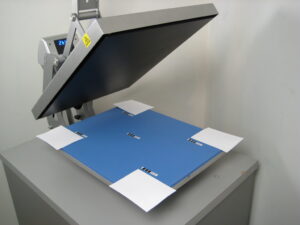
Use a temperature gun or test strips to see how hot your press is, thereby ensuring your settings are correct. Photo courtesy of STAHLS’ Transfer Express
Pressure settings are another common culprit. Scorching often occurs when the pressure is set too high, especially when using smaller platens where the pressure is concentrated over a smaller surface area. Adjusting the pressure for the platen size can make a significant difference. When in doubt, consult your heat press manufacturer for guidance on fine-tuning your settings.
Testing represents another effective way of preventing scorching. Always test your heat settings, including temperature, pressure and dwell time, on a sample garment or inconspicuous area of a garment you’re planning on decorating before committing to the entire job. Taking the time to test can save you from costly mistakes and wasted materials.
Accessories for Preventing Scorching When Custom Decorating
The right tools and accessories can also play a big role in minimizing scorching. Using silicone cover sheets or upper platen protectors creates a barrier between the heat platen and the garment, which helps prevent direct contact that can lead to press marks or discoloration. Note, not all transfers are compatible with these covers, so it’s important to test how they affect application time and adhesion.
Smaller platens can also be useful for isolating print areas. For example, when applying a left chest logo to a performance polo, using a 6-inch-by-6-inch platen guarantees only the necessary area is exposed to heat, minimizing scorching on the rest of the garment. Heated lower platens, which apply heat from the inside out, are another valuable tool. These are especially helpful when applying dimensional products, like patches or emblems that require high heat and dwell time.
Temperature accuracy is equally important. Using a temperature gun or test strips to check how hot your press is, ensures the actual heat matches the settings, preventing scorching or misapplied transfers.
Troubleshooting Scorching Problems When Custom Heat Pressing
Even with the best preparation, accidents happen. If you find yourself with a scorched garment, though, don’t panic—there are ways to salvage it. Using a small handheld heat press or a household iron on a smooth, flat surface at a low heat setting, for example, can help feather the edges of a press box, creating a softer transition and reducing the mark’s visibility. This technique may not work for every fabric or every level of scorch severity, but it can be a lifesaver in many situations.
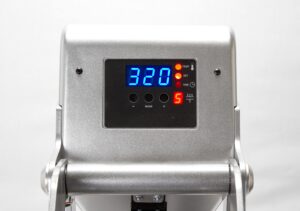
It’s critical temperature, pressure and time are all set correctly to ensure your transfers adhere without damaging the underlying material. Photo courtesy of STAHLS’ Hotronix
For light marks or discoloration, spritzing water over the press box can also sometimes restore the garment’s appearance. This is especially the case with cotton T-shirts, where the press box may be due to loss of moisture, not actual scorching.
While not foolproof, these methods offer a way to recover garments that might otherwise be discarded.
Fortunately, advancements in heat printing technology are making it easier than ever to avoid scorching. Low-temperature heat transfers are increasingly popular, providing reliable adhesion without requiring high heat. Additionally, heat presses with smart temperature controls and heated lower platens offer greater precision and consistency, which helps decorators avoid issues caused by fluctuating heat or pressure.
Blank apparel manufacturers are also stepping up by creating heat-resistant options that give decorators more flexibility. These innovations make heat printing even more versatile, allowing decorators to work with a wider range of fabrics and applications.
Key Takeaways to Preventing Scorching When Heat Pressing
- Understanding your materials is crucial to preventing scorching, as different fabrics react to heat in unique ways.
- Adjusting temperature, pressure and time settings ensures that your transfers adhere properly without damaging garments.
- Investing in tools like silicone cover sheets, smaller purpose-built platens and heated lower platens can significantly reduce the risk of scorching.
- Testing your settings on sample garments and checking temperature accuracy with a heat gun or test strips are small steps that can save time and money.
While scorching can feel like a frustrating drawback when heat printing, it’s also an opportunity to showcase the adaptability of this versatile technology. Heat printing stands out as one of the most flexible decoration methods available, capable of accommodating various fabrics, designs, and application needs. By understanding your materials, refining your techniques, and leveraging advancements in technology, you can confidently navigate challenges like scorching and continue delivering professional, high-quality results.
Through proactive measures, attention to detail, and a commitment to learning, you can turn the challenge of scorching into an opportunity to refine your craft and grow your business.
Dalaney Bradley is a veteran content marketing specialist with long-time custom transfer supplier STAHLS’ Transfer Express (transferexpress.com) and heat-press manufacturer STAHLS’ Hotronix (hotronix.com).
Updated 7/23/25