Go to any industry tradeshow or visit an actual screen-printing shop, and your eyes will naturally be drawn to the press, or presses there. This is true whether the shop in question employs a single manual press or is running multiple autos.
The reality, though, is that a press on its own will only get you so far: that there is a host of other pieces of equipment helping prep and otherwise process screens, cure ink, you name it.
“In my opinion, there’s really no such thing as ‘ancillary’ equipment,” says Alex Sroka of Anatol Equipment (anatol.com). “It’s easy to think of the screen-printing press as the star of the show because it’s where the actual printing happens, but that doesn’t mean your flash cure unit, conveyor dryer and exposure unit are just supporting players. They’re all equally essential to achieving high quality results.”
“Often overlooked is that high-quality ancillary systems are as critical as a high-quality press in achieving top-quality, long-lasting images on printed garments,” agrees Mark Vasilantone, president of Vastex International (vastex.com). “Even garments that appear perfect may begin falling apart after several washes if not flashed and cured consistently.”
Equally important, the design and technologies that go into the operation of many of these pieces of equipment can make a huge difference in terms of both energy consumption and ease-of-use: things that might not be uppermost in your mind when cruising a trade show or researching online but can make all the difference in the world once they’re up and running.
In the words of Workhorse Products president, Tyler Dummett (workhorseproducts.com), “These items may seem less significant, but they play a crucial role in ensuring the efficient operation of your printing business.”
“Investing in technology upfront can save you money long-term,” agrees Cristen Sousa of ROQ.US (roq.us). “The right equipment can prevent you undercuring your ink and having it wash out or scorching a garment, and often helps reduce training expenses for current and new operators as well.”
What follows is an introduction to two of screen printing’s most important supporting players, flash units and dryers. In part 2 of this two-part series, we’ll look at exposure units, washout booths and the growing importance of direct-to-screen, or DTS. For an overview of the ins and outs of choosing the correct press, click here.
Screen Printing Flash Units
So close to the center of action they could almost be considered a part of the press themselves, flash units are responsible for gelling, or partially curing the ink midway through the printing process. This is especially important when applying, say, a white base layer with an eye toward bringing out the rest of the colors in a design on a darker garment.
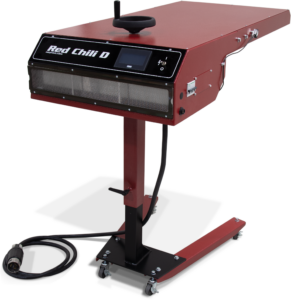
This M&R quartz flash unit includes three independent curing zones.
Factors to keep in mind when considering a flash unit are whether it’s been configured for use with an automatic or manual press (or can be used with both); the type of heating unit it employs; and how it’s regulated, or controlled. Many manual units still produce heat by employing an infrared panel; units configured for use with autos typically employ quartz bulbs. Infrared units are typically less expensive. However, they also cure or gel the ink slower than is possible using higher-wattage quartz bulbs.
Something else to keep in mind: in operation, the heating element in an infrared system is always on. It’s also very hot, creating a potential safety hazard. Quartz systems, on the other hand, only go on when they’re actually flashing, either automatically, when integrated into an auto press, or via a foot pedal, thereby cutting down on energy costs in the long run: a nice perk given the fact that quartz bulb units, again, are substantially more expensive.
Another benefit of the quart flash, Anatol’s Sroka says, is that the bulbs are divided into multiple zones. “If you only need to cure a small image, you can deactivate the bulbs you don’t need, saving energy and money,” Sroka says. “If you want to save up front, an infrared panel flash will probably have a lower price tag. If you want to save over the lifetime of the flash, quartz is the way to go.”
Which is not to say there isn’t still a role to be played by infrared flash units. Per Vastex International’s Vasilantone, whose company offers both types of systems, “Infrared is more suited for manual presses where you have time to wait for an 8-12 second flash…They do take some time to warm up, but once on, they stay on. This will help with the longevity of the unit, and you can find quality flash units with 15-year warranties on the infrared panels. That said, not all infrared panels are created equal. If you look underneath, some have very few coils that are spaced far apart. This creates hot and cold spots resulting in uneven temperatures.”
Something else to keep in mind: as noted earlier, when flashing a base layer, the goal is not to cure the ink entirely, but cause it to “gel” to a point where it’s stable but still a bit tacky, thereby allowing it to bond well to the next layer, or layers of ink. This in turn means requires able to carefully control the amount of heat being applied by adjusting the temperature setting on the flash unit; adjusting the distance between the flash unit and the garment being decorated (around 2 to 3 inches above the ink); and regulating the amount of time each garment spends at the flashing station.
Flash units range in size from 16-by-16-inches to 18-by-18-inches or 18-by-24-inches. Bases with casters allow operators to move them from one press or station to another with ease. Also look for an easy-to-use, reliable height-adjustment system. Many units include a swing-away feature as part of the base or stand as well, making it that much easier to get the unit out of the way when, say, working with a static platen.
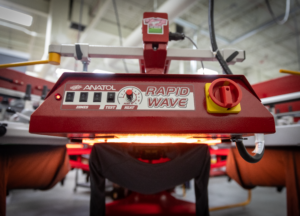
Being able to dial in the correct distance between a flash unit and the garment being flashed is critical to gelling the ink correctly. Photo courtesy Anatol
For those running autos, implementing a flash unit that meshes well with whatever kind of press you’re using is another important consideration. “Investing in the right technology can offer a competitive advantage,” ROQ.US’s Sousa says. “If you’re pairing a flash with your automated press, try to find a flash that is able to communicate with your press for signaling on/off. In addition, flashes with digital parameters can often make it easy to determine the proper time-temperature you are targeting.”
Bottom line, per Workhorse Products’ Dummett, finding the right flash unit for your shop requires matching it to your particular production needs. “A key component is the balance between function and speed,” Dummett says. “Some flashes allow you preserve a printhead (color) by working in conjunction with it, but this option decreases output. Others work independently of the printhead and while you sacrifice a color, this set-up maximizes your output. Ultimately, your flashes need to be efficient and effective at meeting the specific requirements of the ink and garment you are printing on.”
Decorated Apparel Conveyor Dryers
Dryers, in addition to serving a similar function to a flash unit, i.e., curing the ink after the design has been printed, also come in a variety of types and sizes. Don’t be fooled, though, by their boxy looking appearance. There’s more to these systems than meets the eye.
For starters, as is the case with flash units there are two very different types to choose from: gas or electric, with gas dryers preferred by larger shops due to their higher curing capacity and electric dyers preferred by smaller outfits. In addition to higher cost, gas-powered units, which include a blower to circulate heat throughout the curing area, require a dedicated gas line and tend to take up a lot more room. Electric units, on the other hand, are less expensive and much less complicated to set up, though on the downside, the infrared heat generated by an electric unit can be hard to distribute evenly, increasing the risk of scorching.
Per Vasilantone, “Gas dryers are very consistent and will run at a lower temperature, requiring a long tunnel to fully cure the ink.” Vasilantone adds: “These units need to plumb into a gas line, so once the dryer is in place, it will need to stay there. There is also a significant initial cost of installing a gas dryer…Electric dryers will run at higher temperatures so they will cure inks in less time, allowing for a much smaller footprint. They also can be moved around, whether that is to clean underneath or rearrange your shop.”
Beyond that, pretty much all conveyor dryers include a belt-speed control to help regulate the amount of heat applied to the garments going through—faster speeds, less heat; slower speeds, more. Going up the scale in terms of size, sophistication and price, you also get temperature controls, a variety of different heat sensor and the ability to pre-set and saving various belt-speed/temperature combinations. This is important. One the one hand, you want to heat the entire ink layer, or layers of the design to the correct curing temperature—typically around 320°F for most standard-cure plastisol ink. On the other you want to avoid scorching the ink or the underlying garment.
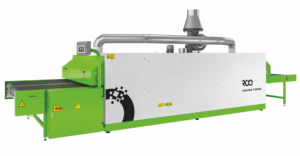
The split belt on this ROQ SAHARA dryer provides maximum flexibility for multiple production runs.
“When running different garment types or inks through the same dryer, it’s important to consider things like zone control, split belts for running at different speeds, or belt width/infeed length if you’re running multiple machines into a dryer,” Sousa says. “Most dryers can be customized, so if you’re a shop looking to grow it’s important to look into the options for future upgrades. A shop that has more width available in terms of space may run their belt slower with a smaller chamber or a shop that is narrow but has considerable length may resort to a smaller belt width with an increased length in chamber.”
Speaking of size, bigger is not surprisingly better, especially if your shop’s primary concern is production capacity. Larger systems also provide better thermal stability, i.e., are less susceptible to temperature changes due to things like the ambient temperature in your shop or the moisture content of the inks or garments being processed. Of course, the downside to size is the fact a larger system with a larger and longer belt will take up a lot more space in your shop. It will also cost more.
“A larger dryer will prevent bottlenecks in your production and increase the output capacity of your entire shop,” Dummett says by way of summary. “When considering a larger dryer, keep in mind the following: belt width, oven chamber, rate of production and power source,” he adds.
Speaking of belt widths, Vasilantone says, “When purchasing a dryer, specify a wider belt if possible. If you purchase a modular dryer, you can upgrade its length but not its width. Wider belts allow for multiple rows of garments to be cured at the same time, which is great if you have more than one press running through the same dryer.”
Something else to keep in mind when thinking about belts is belt infeed length, i.e., the length of belt extending beyond the dryer itself, and the option of a split belt.
“Belt width and infeed length is especially important if you’re feeding multiple presses into a single dryer,” Sroka says. “You’ll work more efficiently if you can lay two garments side by side on the belt. A split belt dryer will allow you to run the belts at different speeds. If you have two presses printing two different ink types,” he adds, “you can cure them both properly and simultaneously with a single dryer. A split belt dryer will also allow you to run the belts in different directions, so it’s a good fit if your shop layout dictates that you have presses on either end of the dryer.”
Whatever the case, as with flash units, dryer units are an area in which you don’t want to cut costs. Reliable consistent heat and a rock-solid precision conveyor are vital to ensuring the designs you put all that time and effort into creating and printing perform well out in in the real world on the garments to which they’ve been applied.
Ed Note: To see Part 2 of this two-part series on screen-printing accessory systems, including exposure units, washout booths and DTS, click here. For an overview of the ins and outs of choosing the correct press, click here.
Updated March 15, 2024