The screen-printing business can be both funky and inspiring. On the one hand, tales abound of ex-rockers who started out decorating T-shirts for whatever band they happened to be in at the time ending up creating a multi-million-dollar business. On the other, there are the horror stories—tales of failed print runs, bankruptcy and broken dreams.
To avoid the latter, as is the case with pretty much any business endeavor, one of the keys is having the right equipment, of which there is plenty when it comes to screen printing: think screens, squeegees, washout booths and, of course, the press, or presses themselves.
Of these, arguably the single most important piece of gear is the latter, i.e., the press. Not only because it’s the most expensive and takes up the most room, but because it serves as a kind of foundation for everything else. Sub-par screens or squeegees? Bummer. However, you can easily swap them out for something better. Chronic registration problems or the inability to execute the kinds of designs your customers are asking for because of the limitations inherent in that supposedly gee-whiz auto you just purchased? Sorry, you’re pretty much stuck.
What follows is a brief overview of a few things decorators need to be prepared to look out for when considering a new screen-printing machine—whether you’re just starting out printing T-shirts for your latest band or church group, or making the jump from startup to major decorator.
(For more on such critical ancillary items flash units and conveyor dryers, click here. For more on the importance of having the right exposure units, direct-to-screen systems and washout booths, click here.)
Manual Screen-printing Presses
To begin with, never forget that no matter what system you choose to go with, you and your operators are going to be spending countless hours working with it. Therefore, as you are evaluating any given system, imagine what it’s going to be like generating product while employing whatever features it may have to offer. This includes everything from the specific kinds of the mechanism employed for getting screen in register and then keeping it there to the “feel” of a system as a whole.
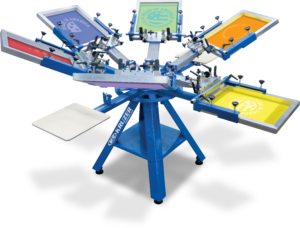
The comprehensive fine-tune features on this M&R manual system will go a long way to helping facilitate setups. Photo courtesy of M&R
Other factors to consider, depending on the kinds of production runs you have in mind, include the number of stations/colors you want to work with and whether or not to go with a manual system versus an auto.
Alex Sroka of Anatol Equipment, for example, notes that when evaluating a manual screen-printing press, one of the biggest factors to look for is smooth, easy movement. “Manual printing with its repetitive movements will take a toll on your body…no matter what press you’re using. You don’t want a press that’s going to be fighting you and exacerbating the physical strain,” Sroka says. “Test the weight of rotating the pallets and the resistance when raising and lowering screens. Many presses offer adjustable spring tension in the print heads, which is a nice feature to have. Check the height of the pallets and screens as well. If they’re too high or too low when loading shirts and printing, forcing you to bend or reach excessively, it can be uncomfortable at best, and affect your print speed and quality and lead to long-term injury at worst.”
Similarly, when it comes to the printing process as a whole, be sure to pay close attention to the question of registration. On the one hand, depending on the sophistication of a press’s clamping and fine-adjust features, you may find yourself spending far more time on setups than you might otherwise want. On the other, you may find yourself with a system that, despite a wealth of fine-tune features, refuses to stay in registration when it comes time to do the actual decorating.
With this in mind, Maggie Sobilo of M&R Printing Equipment says, “In the case of both a manual and an automatic press decorators should look for a machine that has good rigidity in the print-stations and pallet arms, and can maintain accurate print registration from the first print to the end of the run.”
Sobilo adds another important consideration for automatic press buyers, in particular, is finding a machine with an accurate screen pre-registration system in order to achieve faster setups with reduced downtime. “A lesser-quality press that suffers from excessive pallet deflection or that doesn’t hold registration will take longer to setup and suffer from smudging between colors, causing a blurred print requiring the operator to stop to clean the backs of the screens…remember, if your press isn’t turning, you’re not earning,” Sobillo says.
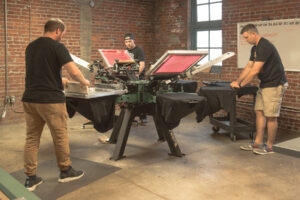
When considering a new screen-printing press for T-shirt decorating, imagine what it’s going to be like actually working with the system in your shop. Photo courtesy of Vastex International
Along these same lines, Mark Vasilantone, president of Vastex International says, “For manual presses, you want a press that will hold registration for repeatable results…There are two basic designs: one is a sturdy, heavy-duty frame and structure, which equates to low- or no-flex between the pallet and print head. The moving parts use precision ball bearings so there is no movement other than the intended rotation.
“In the other design, [which] does not require such a heavy-duty structure and precision bearings, the presses have ‘floating heads.’ With these presses, the print head and screen ‘float’ to the pallet/shirt. Regardless of flex in the structure, the screen and pallet/shirt become essentially tied together with the screen lowered into position.”
In either case, Vasilantone says, look for a press that offers micro-registration controls on the print head, thereby providing you the ability to move the pitch of the screen from side-to-side or front-to-rear without loosening the screen clamp. “Having this feature will significantly cut down on set-up time when lining up each screen or color on multi-colored jobs,” Vasilantone says.
Speaking of pallets, Anatol’s Sroka notes another important thing to watch out for when evaluating a manual press is pallet deflection. To achieve good results, Sroka says, particularly with multicolor prints and highly detailed jobs, it’s very important that the pallet and screen remain level to one another during printing.
“As you apply pressure with the squeegee, the pallet should not give. The squeegee movement should be on plane with the pallet so you’re depositing ink consistently every time. Look for a manual press that has robust pallet arms and heavy-duty steel construction, while still being light and easy to operate.”
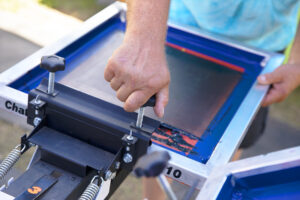
A closeup view of the fine-adjust mechanism on a Vastex manual screen-printing press. Photo courtesy of Vastex International
In addition, Sroka says, “The ability to adjust the angle of your screens relative to the pallets, ensuring you maintain perfect pitch, is another helpful feature to look for. When you’re printing manually, the human body is inevitably going to cause variation from one print to the next. For maximum print consistency, you want a press that’s going to provide a sturdy, stable printing platform.”
Beyond that, as is the case with any piece of capital equipment, look for rock-solid construction and robust materials overall. Again, the whole point of the exercise is to purchase a piece of equipment you can work as hard and fast as possible. You’re therefore going to want it to be able to stand up to anything and everything you throw at it.
As an example, Vastex International’s Vasilantone notes that with lesser-quality presses, especially ones with nylon bolts, it is possible to lose registration in the middle of a big job, which means lost time and poorly printed product while stopping to realign the colors. “Such events could potentially lose a customer and future business,” Vasilantone says.
In a similar vein, Sroka says settling for a lesser-quality press usually means you’ll be getting a machine with lighter-duty construction. “The industry’s most reliable presses are made out of steel. They distribute weight effectively and handle the inertia of the pallet rotation and indexing with minimal vibration. A little bit of vibration can have a big impact on your print quality. Vibration can affect the press’s ability to hold registration and deliver consistent prints,” he says.
Automatic Screen-printing Presses
Moving on to automatic screen-printing presses, many of the things to look out for are the same as with their manual brethren—think rock-solid construction; top-quality, easy-to-work with clamping and registration; and an attention to detail in keeping with your investment. If time is money with a manual press then time is money by an order of magnitude more with an auto.
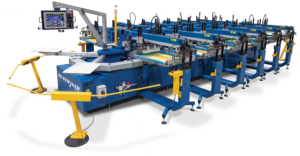
An automatic screen-printing press with as many stations as the M&R Stryker increases a shop’s flexibility at the same time it increases productivity. Photo courtesy of M&R
Also look for features like the ability to adjust squeegee angles, pressure and/or speed, which can adversely affect your prints and production times, Vasilantone says.
Similarly, while pneumatic operation was the long standard for automated screen-printing presses, servomotors are becoming increasingly popular at the top-end as a means of maximizing precision and reducing maintenance and downtime.
“Traditionally, automatic presses have used air compressors and pneumatic components for operation,” Sroka says, adding, “It’s true that pneumatic components are often cheap and easy to replace. However, they’re not always so easy to diagnose when issues occur. You might not even discover an air leak exists until it’s already cost you thousands of dollars. That’s why most of the top manufacturers have made efforts to reduce their machines’ reliance on compressed air. Automatic presses powered by electric motors have fewer moving parts, require less maintenance and operate more efficiently.”
Something else to be aware of: at the top end there are also now any number of systems integrating both screen-printing and direct-to-garment (DTG) printing in an effort provide yet more flexibility in terms of a shop’s production capabilities. The idea here is to be able to make possible the best of all worlds with an eye toward creating the widest variety of prints in combination with increased flexibility and the highest imaginable print quality. Examples, include the M&R DS-4000 Digital Squeegee Hybrid Printing System and the ROQ HYBRID from ROQ US.
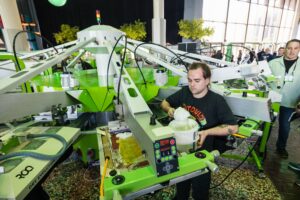
As with a manual system, you’re also going to want your operators to feel comfortable doing their jobs on an automatic press. Photo courtesy of Impressions Expo
As for the question of when and whether to go automatic, the answer will ultimately depend not only on anticipated production volumes, but the time and effort required to integrate a decidedly more complicated piece of equipment into your company’s production processes.
“There are a great number of factors that come into consideration to determine the right time for a business to move from a manual press to an automatic, that include the need for higher volume capacity, trouble finding qualified staff or an owner-operator who wants to reduce the hours they spend pulling a squeegee each day, so they can remain focused on growing their business,” M&R’s Sobillo says. “A couple of additional factors for consideration before investing in an automatic is [whether a company has] the work, both now and into the future to keep the press running, and if the rest of the shop infrastructure is capable of keeping up with the increased volume.”
“When you transition from a manual press to an automatic, it’s easy to think of the automatic press as reducing the amount of labor in your shop, but that’s only partly true,” Anatol’s Sroka says. “Yes, you won’t be spending time pulling a squeegee anymore. But overall, the work you and your human employees are doing isn’t really being reduced, it’s being changed.”
Specifically, Sroka says, when you add an automatic press, you’ll be turning around more jobs in less time. Pre-press work will increase. You’ll be coating, drying, exposing, washing out and reclaiming more screens in a day. You’ll have more orders to process, and you’ll need tighter control over your production scheduling, your purchasing, staging and shipping.
Moving on to the question of the number of colors and stations a press should offer, the answer obviously depends on the needs of each shop. That said, as a general guide, Sobilo says, “The majority of manual presses sold for manual screen print production are either six-color/six-station or six-color/four-station models.” According to Sobillo, while there are manual presses available with a greater number of colors and stations available, they tend to be heavy to spin and are more often used for producing a smaller quantity of sample prints.
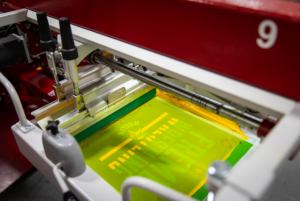
A closeup view of a servo-driven Anantol screen-printing system. Photo courtesy of Anatol Equipment Manufacturing Co.
As for autos, Sobilo notes an eight-color/10-station automatic press is required to produce a five-color image with an underbase, a flash cure unit and a cooling station. She adds a 10-color/12-station press is also a great option due to the fact it allows for printing simulated process designs and/or to have multiple two- or three-color jobs set-up on press at the same time.
“Rarely would I advise buying an automatic press with fewer than six print heads,” agrees Sroka. “Consider that you’ll often need to dedicate a station to printing underbase, and that a flash cure unit will take up one of the print heads. You may not be doing more detailed work like four-color processes now, but might you add it in the future? You’ll need a press with enough stations to accommodate that kind of work, plus at least one flash and a white-ink station if you’re printing on dark garments. You may want to add an accessory like an in-line heat press, roller squeegee or cooling fan, which take up additional print heads.”
Similarly, Vastex International’s Vasilantone says, “Factors to consider are the volume and complexity of the anticipated orders. Simple one-color T-shirts for kids’ sports teams may not require more than a four-station press. But complex jobs, like multi-color prints, require more. To run a true four-color job, six stations may be needed to allow for the four colors plus an underbase on dark shirts and a white highlight.”
Bottom line: six-color presses are not just for six-color jobs, Vasilantone says. Extra print heads are beneficial for setting up multiple jobs at the same time or leaving a job set up in case additional prints are needed after the order is delivered. “It is important to plan for future growth. Look for presses that are fully expandable with additional stations and/or colors to allow for a higher volume of work without having to buy a larger press.”
The Future of T-shirt Screen Printing
Finally, for those wondering about the future of screen printing in light of the progress currently being made in the areas of DTG and DTF (direct-to-film) printing, it’s safe to say, given the advantages it still offers, it’s not going anywhere anytime soon.
“Each method certainly has its place,” Sroka says. However, he adds: “Screen printing remains the most cost-effective solution for printing high volume. While other methods are catching up, for the foreseeable future you’re unlikely to be able to print 1,000-plus shirts per hour with a single machine using any method other than screen printing.”
“Screen printing is universal, diverse and versatile. You can print on almost any fabric if your flash and cure temps are set appropriately,” Vasilantone says. In addition, he says that while a well-rounded print shop will offer multiple decorating options, “especially with mid- to high-volume jobs, screen printing allows higher output per hour at lower cost per piece, translating into greater profits for the shop owner. A single operator on an automatic can produce 400-500 multi-color prints per hour with ink costs at pennies per shirt.”
“There is no argument these newer printing technologies have taken a bite out of traditional screen-printing, but so far it has been a very minor share of the overall printed apparel production,” Sobilo says. “The higher production capacity, lower cost per print, the availability of special effects and the versatility to decorate a wide variety of fabrics should ensure a long runway ahead for the screen-printing process.
Ed note: Again, for more on such critical ancillary items flash units and conveyor dryers, click here. For more on the importance of having the right exposure units, direct-to-screen systems and washout booths, click here. For more on the importance of such “odds and ends” as screen frames and squeegees, click here.